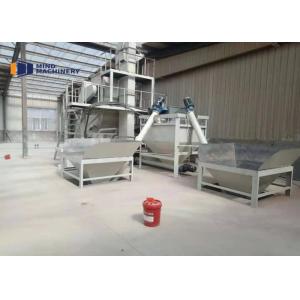
Add to Cart
Output capacity | 10-30t/h |
Floor Area | 150m2 |
Total Power | 75kw |
Operators | 3-4 persons |
Height | 8.5m |
Warranty | 12 months |
Operation Mode | Full automatic |
Main Material Batching and Weighing | Automatic&manual |
Packaging System | 25kg, ton bag, bulk packaging |
Installation and Debugging | Engineers available working abroad |
Application | Drymix mortar and putty powder |
Investment Scale | Small and middle business |
I. Dust collecting system
Drying system of dusting collecting system adopt primary gravity dust collecting and secondary bag dust collecting method. Dust particle could be 100% recycled without pollution.
Source of dust coming from any material during conveying is collected with different kind of dust collecting equipments, filter bag adopts imported material for high standard of dust removing, which can effectively control dust discharge to reach or exceed national environmental protection level standard.
II. Electrical control system
Electrical control system of Xitong brand dry mortar mixing plant adopts double pc sync control method, which is mainly composed of 2 sets of high stability IPC, Mitsubishi PLC, weighing unit from international famous brand and electrical components, through combination with professional control software of own intellectual property rights, it can realize auto running and production management.
In double pc sync control system of dry mortar mixing plant, 2 sets of computer realize control of whole production line synchronously or separately, when 1 of them breaks down, another could control on automatically without manual to finish production control and management without stop, which minimizes the chance of equipment shut down caused by IPC failure.
In batching process, control system would real-time display all kinds of data and operation and batching process in cartoon, with easy operation, friendly human-computer interface, reliable running, and high batching accuracy functions.
Item | Equipment | Functions |
1 | Material in-charge hopper | for charging material to bucket elevator. |
2 | Bucket elevator | Lifting materials to pre-mix silo. |
3 | Double shaft non-gravity mixer | uniform mixing of materials, special paddle sets suitable for fiber mixing. Big double door could accelerate material discharge uniformly, paddle sets are optional according different type material. |
4 | Finished product silo | for storing finished material and secondary mixing of pre-packing material. Finished product silo is available for connecting automatic metering packer and manual discharging valve |
5 | Automatic metering packer | packing finished product by automatic weighing, high accuracy. |
6 | Pulse dust catcher: | absorb the dust during production process, mainly used for de-dust from material in-charge hopper and packer. |
7 | Control cabinet | includes instrumentation and PLC control for controlling electrical switch of the whole production lines. |
8 | Compressor | Produce compressed air for the whole air compressing system |